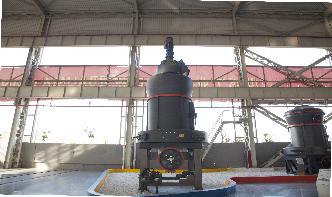
Improving Productivity and Energy Utilization in Steel ...
However, annealing is also a main energyconsuming operation in the cold rolling stage; it consumes a huge amount of energy and resources, such as water, electricity, and coal gas and protective gas. Thus, the batch annealing process is one of the bottlenecks at most steel plants, and improving its efficiency becomes crucial to increase a steel company's profitability and energy utilization.