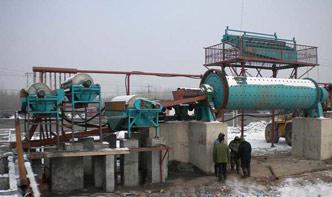
How to improve cement plant process for better cement quality
In cement grinding process, although the specific surface area needs to be measured every once in a while, it has no close correlation with the cement strength and cannot reflect the distribution of cement particles. Therefore, the specific surface area of cement shall not be used as the single factor on quality control of cement milling. The particle size distribution of cement clinker is ...