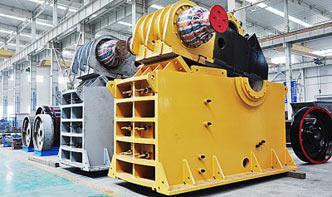
Roll Compactor: The Ultimate Buying Guide
d) Roller compaction technology guarantee high production . Roller ... The large particles remain in the mill for further crushing; ... This is what consequently leads to the transformation of powders into compacted ribbons, flakes and sometimes the sheets. So, ...