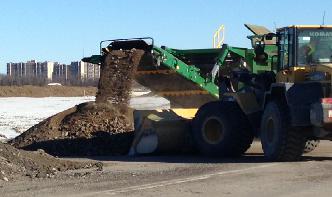
A case study on energy and exergy analyses for an ...
· 1. Introduction. World cement production is about billion tons in 2019 and cement plants consume about 2 percent of world electrical energy in the grinding process, .The total electrical energy that is consumed in cement companies is about 100 kWh per 1000 kg of cement, and twothird of this amount just consumes in raw material and cement mill units .