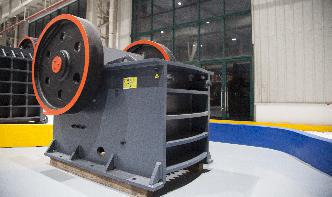
sponge iron process ppt
The process of sponge iron manufacturing involves removal of oxygen from iron ore. When that happens, the departing oxygen causes micro pores in the ore body, turning it porous. When the eventual product is observed under a microscope, it resembles a honeycomb structure, which looks spongy in texture. Hence the name sponge iron. More Details. Ppt Presentation On Sponge Iron .