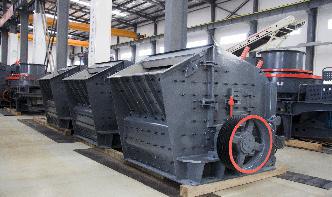
The size requirement Coke (1)
The normal coke oven practice is to crush coals about 80 per cent through 1/8 in., such crushing producing maximum percentage of material on 4 in. size. With finer crushing the oversize on 4 in. diminishes gradually but the percentage of material in the intermediate sizes 4 in.3 in., 3 in.2 in. and 2 in.ltz in. steadily increases. The cumulative percentage of total material on 1 % in ...