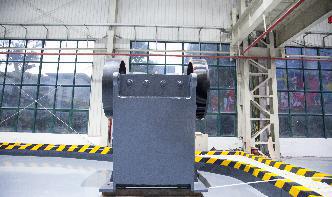
CEMENT INDUSTRY
GLOBAL CEMENT CONSUMPTION ... ground in mills to produce cement powder. ... Cement accounts for 83% of total energy use in the production of nonmetallic minerals and 94% of C02 emissions. Energy represents 20% to 40% of the total cost of cement production.