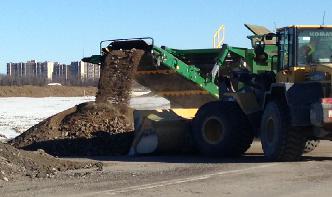
Mineral Drying
Extracted ore, no matter the mineral, is typically first crushed, and then must go through a beneficiation process to remove the unwanted impurities. Beneficiation can vary significantly from one ore type to the next. In most cases, however, beneficiation is carried out through a wet process that necessitates a subsequent drying step.