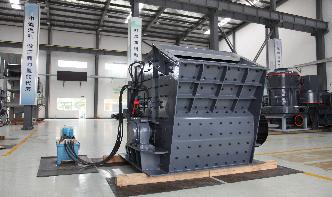
flotation process ores
The primary methods of potash ore processing are flotation Productions Units 1 2 and 3 process the potash ore by flotation and Production Unit 4 uses the. Froth flotation process Australia Innovates Powerhouse. Froth flotation process 1904 process for separating mineral ores At the end of the 19th century metal prices had slumped and around every Australian mining town ...