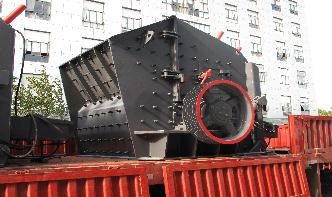
Hydrogen as a Clean Alternative in the Iron and Steel ...
· However, the production of these materials has significant environmental impacts. As of 2017, the iron and steel industry produces seven to nine percent of the total global GHG emissions. The carbon emissions are directly related to iron ore reduction, a process that produces usable pig (crude) iron to be turned into crude steel.