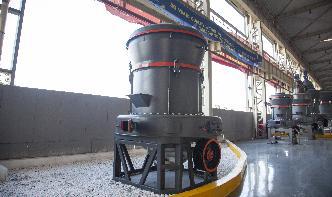
TIVAR® 88 Lining Solutions
coal types, some with high volatility properties prone to selfcombustion. Coal is fed into the mills through carbon steel standpipes with an inside diameter of 600mm (24") and varying lengths and geometries • ProbleM The power plant was having flow problems associated with their coal handling system standpipes feeding the coal mills.