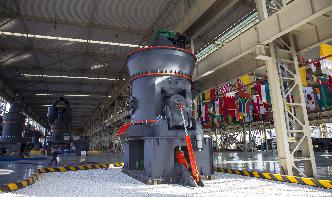
Safety Guidelines for Coke Ovens Coal Chemicals
coal charging, coal carbonization, coke pushing coke cooling. Coke oven emissions contain cancercausing polynuclear aromatic hydrocarbons, along with toxic gases and vapours such as benzene, hydrogen sulphide, carbon monoxide, ammonia etc. 2. Scope: This recommended guideline is applicable to Coke ovens By