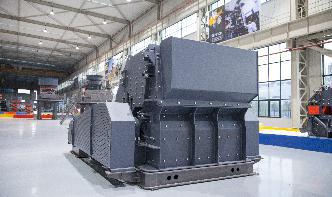
Calculation Of Ball Mill Design
Ball Mill Design/Power Calculation. The basic parameters used in ball mill design (power calculations), rod mill or any tumbling mill sizing are; material to be ground, characteristics, Bond Work Index, bulk density, specific density, desired mill tonnage capacity DTPH, operating % solids or pulp density, feed size as F80 and maximum 'chunk size', product size as P80 and maximum and ...