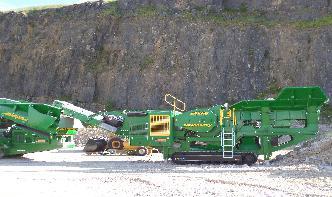
The first Electric Arc Furnace waste heat recovery ORC ...
· The first Electric Arc Furnace waste heat recovery ORCbased system is in commercial operation at Feralpi steel plant in Germany Thanks to the successful performances recorded, a contract for a second similar plant in Italy was recently awarded to Turboden.