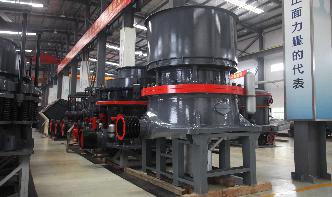
Deatil working process of a iron ore crusher
Deatil working process of a iron ore crusher Products. As a leading global manufacturer of crushing, grinding and mining equipments, we offer advanced, reasonable solutions for any sizereduction requirements including, Deatil working process of a iron ore crusher, quarry, aggregate, and different kinds of minerals.