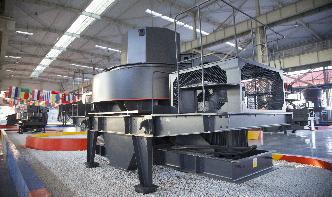
Iron Ore | McCreath Laboratories
Iron Ore. Iron ore naturally occurs in rocks and minerals. To yield metallic iron (Fe), it undergoes a heating process with a reducing agent such as coke or anthracite coal and a fluxing material such as limestone. In the steelmaking industry, 98% of production uses iron ore. Because this material is instrumental to the steel industry ...