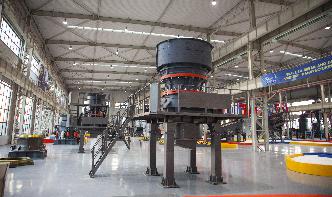
PARTICLE SIZE REDUCTION TECHNIQUES
· BALL MILL Principle: The ball mill works on the impact between the rapidly moving ball and the powder material, both enclosed in a hollow cylinder. Thus, in the ball mill, impact or attrition or both are responsible for the size reduction. Fig: Ball mill 13 14. Working: The drug is filled into cylinder 60% of the volume.