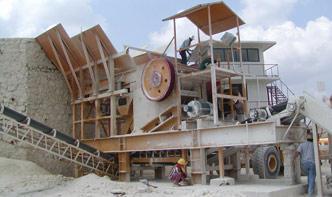
Blast furnace process
· These hot gases rise up in the blast furnace and cool down. From a maximum of 2000 °C at the level of the hotblast nozzles (tuyere), the temperature decreases to around 200 °C up to the throat. At this temperature, the filled charge are first dried and preheated. This zone of the blast furnace is therefore called the preheating zone.