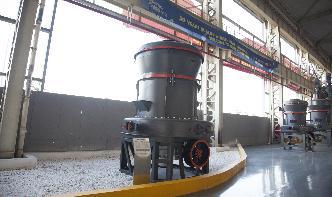
Process for the extracting oxygen and iron from iron oxide ...
We claim: 1. A process for producing oxygen and metallic iron from an iron oxidecontaining mineral comprising the steps of: (a) contacting the mineral in finely divided form with water and hydrochloric acid, hydrogen chloride vapors or a mixture thereof to dissolve hydrochloric acidsoluble iron in the mineral and produce a solution containing an insoluble solid residue;