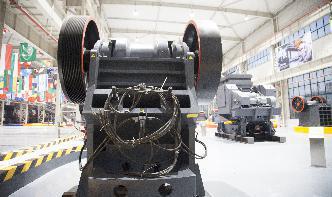
Energy and Cost Analysis of Cement Production Using the ...
In Nigeria, approximately 40 to 50 per cent of cement manufacturing cost is energy related; each tonne of ce ment requires 60 130 kg of fuel oil or its equivalent and about 105 kWh of electricity, depending on the cement variety and process type employed [10]. Cement produc tion spreads across five geopolitical zones due to the