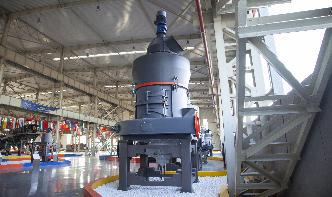
Ore sorting: Efficiently optimise the treatment of ores in ...
Use ore sorting equipment to concentrate ores and cut process costs There are many ways of improving recovery processes for a wide variety of ores using sorting equipment. At STEINERT we always take the same approach: sorting waste rock and ore with low concentrations out from the process at an early stage to save energy and resources and to unlock more enriched ore more effectively.