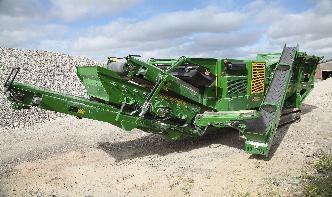
greatwallec
Aug 26, 2016 · Appliion : Cement Plant, Clinker Grinding Unit, Steel Mill, Quicklime Plant Capacity : 21155 t/h. Motor Power : kw. Cylinder length : 3000~6000 mm. CHAENG energyefficient ball mill equipment is new equipment to transform the basis of the traditional ball mill after, It changed the original mill structure, it is possible to reduce energy consumption by 30%, capacity increased by ...