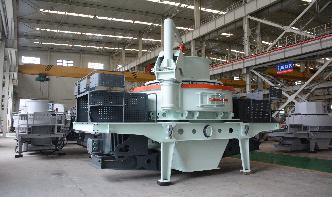
RSE4040 Iron Ore
View RSE4040 Iron Ore from MNMT 655 at San Francisco State University. Engineering RSE4040 Mineral Processing Iron Ore Processing Dr Mark Pownceby CSIRO Mineral Resources, 3 .
View RSE4040 Iron Ore from MNMT 655 at San Francisco State University. Engineering RSE4040 Mineral Processing Iron Ore Processing Dr Mark Pownceby CSIRO Mineral Resources, 3 .
The StepbyStep Process of Producing Iron from Iron Ore. The StepbyStep Process of Producing Iron from Iron Ore. Some years ago, the ancient Egyptians derived iron from the fallen meteorites (or so they say), carved them and made tools and equipment besides jewelry.
Mar 04, 2021 · Separating ferrous metals from nonferrous metals is one of the most important steps in the sorting process. As ferrous metals contain iron, they are attracted by magnets and easily pulled out of the mixed waste stream. In scrap yards, cranes fitted with .
Iron Ore. Efficiently remove silica and alumina contamination to increase efficiencies in steel production. Our iron ore wet processing plants are proven to successfully deal with silica and alumina contamination in the iron ore, resulting in an increase in the Fe value of the iron ore thereby increasing the efficiency of the steel production process.
Cement is manufactured through a closely controlled chemical combination of calcium, silicon, aluminum, iron and other ingredients. Common materials used to manufacture cement include limestone, shells, and chalk or marl combined with shale, clay, slate, blast furnace slag, silica sand, and iron ore. These ingredients, when heated at high ...
how to extract iron from the iron ore, extract iron in an iron furnace, examples and step by step demonstration, iron oxide, coke, limestone, slag, steel Extraction of Iron A series of free IGCSE Chemistry Activities and Experiments (Cambridge IGCSE Chemistry).
Mar 26, 2020 · Magnetite and hematite are iron oxides; however, the extraction of iron from an iron oxide involves a series of steps that begins when mined iron ore is crushed into smaller pieces by a crusher and then washed. The second step in the process is calcination or roasting of the ore, which removes certain impurities, carbon dioxide and other ...
Jun 11, 2019 · Sintering: A Step Between Mining Iron Ore and Steelmaking. The USGS defines iron ore as a mineral substance which, when heated in the presence of a reductant, will yield metallic iron (Fe). It almost always consists of iron oxides, the primary forms of which are magnetite (Fe3O4) and hematite (Fe2O3). It's a major ingredient in steel.
The Ally to Your Iron Ore Processing Plant. Here at Benetech, we dedie our greatest resources to resolving your daily challenges in bulk material handling. To discuss how you can reinforce a safer, more productive iron ore facility, contact us at (630) to .
DETAILS OF EXTRACTION The process of the extraction of iron is carried out by the following steps: Concentration of ore Calcination or Roasting of ore Reduction of ore Concentration of ore: In this metallurgical operation, the ore is concentrated by removing impurities like soil etc. The process involves the crushing and washing of ore.
Sep 25, 2018 · Low grade Iron Ore Beneficiation and the Process of Jigging. Iron ore resources are getting consumed at an accelerated rate because of the growth in the production of iron and steel. Due to this reason the availability of high grade iron ore is reducing and the supply of high grade iron ore to iron and steel plants is declining sharply.
The Latest Developments in Iron Ore Processing –Process 600t/h lumpy iron ore • DMS Cyclone –Only 6mm material for iron ore –360mm diameter cyclone –Process 40t/h per cyclone • Larcodems –90+6mm stones – diameter –Operating capacity of 600800t/h –Efficient separation at SG's as high as /cm3 Dense Media Separation on Iron Ore •
With 5 mines, 4 processing hubs and 2 port facilities, our Pilbara iron ore business is all connected by more than 1,000 kilometres of rail infrastructure. At each mining hub ore from the mines is crushed, beneficiated (where necessary) and blended to create highgrade hematite lump and fines products.
We know that not all Iron Ore deposits are the same and changing commodities prices are placing higher demands on producers to 'sweat the assets' through process improvements, and increase revenues by converting tailings. That's why understanding your project objectives and opportunities is our first step in developing solutions that ...
Apr 10, 2020 · Iron products evolved during this time, beginning with blacksmiths producing wrought iron goods. These tradespeople learned to heat up iron ore, and using a hammerandanvil process, the blacksmiths would remove impurities from the metal and produce a .
The HIsarna steelmaking process is a process of primary steelmaking in which iron ore is processed almost directly into steel. The process is based on a new type of blast furnace called a Cyclone Converter Furnace, which makes it possible to skip the process of manufacturing pig iron pellets, a necessary step in the basic oxygen steelmaking ...
Jun 04, 2015 · Steel is made primarily in a twostep process. In the primary steelmaking step, liquid iron is converted into steel by the basic oxygen furnace (BOF) process, or by melting scrap steel or direct reduced iron (DRI) in an electric arc furnace. Secondary steelmaking is a refining process in which alloying metals are added and impurities are removed.
Jul 11, 2018 · The iron ore production has significantly expanded in recent years, owing to increasing steel demands in developing countries. However, the content of iron in ore deposits has deteriorated and lowgrade iron ore has been processed. The fines resulting from the concentration process must be agglomerated for use in iron and steelmaking. This chapter shows the status of the pelletizing .
Iron ore direct reduction is an attractive alternative steelmaking process in the context of greenhouse gas mitigation. To simulate the process and explore possible optimization, we developed a systemic, multiscale process model. The reduction of the iron ore pellets is described using a specific gr .
Feb 10, 2015 · Many iron ore producers are facing challenging times; processing crude material with rising levels of impurities and a volatile iron ore price. Beneficiation, particularly washing (scrubbing), can be the key to upgrading the ore to earn more per shipped tonne. Highend steel production at a low coke consumption level and a high productivity rate can only be achieved by using highquality ...
Iron ore processing technology: The iron ore beneficiation crushing production line has high degree of automation, high breaking rate, low operating cost, energy saving and environmental protection, and fine grain size. The production line is mainly based on the actual material size and the customer's requirements for product granularity.
Iron Ore to Steel. Raw material for manufacturing the TMT Bar are iron ore, coal, dolomite. In this process raw materials are piled, recovered and mixed in required proportion. The iron ore experiences beneficiation procedure to raise the iron substance. At this point metal fines are gathered to shape a mass of pellets and sinter to improve ...
To efficiently process iron ore for high quality steel production, frequent ore grade monitoring, during all steps of downstream processing, is mandatory. Independent from the ironmaking method, the optimal use of fuels and energy during sintering, pelletizing and direct reduction of iron ore (DRI) needs to be applied to stay competitive and ...
Ore Processing (1518) Global Mining. Processes; Ore Processing; and Minerals and Everyday Life. .... Review the steps involved in processing copper ore, as mentioned in the film: crushing, ..... The objectives of this activity are to learn how iron ore is processed into steel, to learn.
Mar 20, 2017 · Pig Iron. At the beginning of the use of the electric furnace, for the manufacture of calcium carbide and ferroalloys, experimental work was conducted in it upon the production of steel from iron ore. For many years steel and wrought iron have been produced directly from ore on a small scale in the forge, crucible, and reverberatory furnaces ...