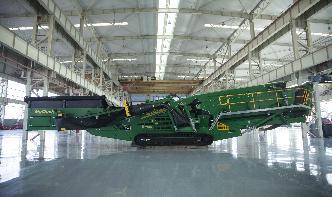
A new inprocess material removal rate monitoring approach ...
· The material removal rates are,,, and g/(mm/s), respectively. Table 4 shows the feature values corresponding to the four spark field images. It can be seen from the figures and Table 4 that the four features of the spark field increase as the material removal rate and grinding depth increase. Because deeper grinding depth ...