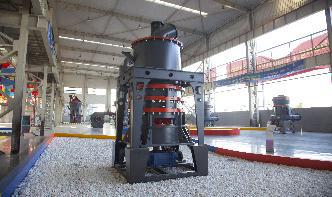
In Grinding, Coolant Appliion Matters
Mar 01, 2008 · Grinding is a thermally dominated process. If done incorrectly, it can lead to surface damage to the work material, and unsatisfactory process economics due to inadequate removal rates and/or excessive wheel wear. Power consumed by the process flows into .